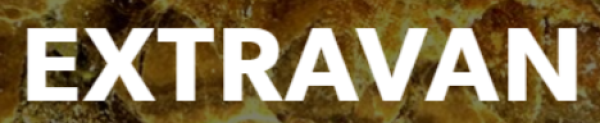
Abstract & Results
The EXTRAVAN aimed at developing novel technologies for production of vanadium in Europe based on Vbearing iron ore and V-bearing steel slag existing in the Nordic countries. EXTRAVAN focused on two major technological approaches. Route A is a “roasting-leaching” route including a novel approach for roasting of Vslag with very high vanadium content. This technology has been developed and demonstrated during the EXTRAVAN project. The industrial partner has contributed additional 35 000 € to make this pilot testing possible. The vanadium yield achieved is as high as 97%. All technical steps from high V-slag to roasting, leaching, AVP precipitation, V2O3 and V2O5 preparation, FeV making have been demonstrated in various scale with a very high overall vanadium yield. The results of the project have been an important and crucial part of the project development of MKOY (FERROVAN).
The second focus (Route B) in the EXTRAVAN was development of a new approach for vanadium extraction using spent PVC waste stream as the chlorination agent. BRGM has demonstrated the concept capability in laboratory scale. High process flexibility has been demonstrated and a high V-recovery yield has been achieved. The technological achievements include a special roasting approach for high V-containing slag for the FERROVAN process aiming for a high overall vanadium recovery yield demonstrated in large pilot scale and a carbochlorination approach using spent PVC waste demonstrated in laboratory scale. The scientific achievements include: - A PhD thesis work (Mikael Lindvall, Swerim/Royal Institute of Technology (KTH), Sweden). - A Master thesis work (Martin Berg, KTH). - Two publications concerning “roasting-leaching” and optimized conditions for vanadium extraction (published). - Two publications on the PVC roasting approach (to be submitted by BRGM). - Over 10 presentations at various international conferences, seminars and workshops including those arranged by ERAMIN (Stockholm/Berlin).
The main conclusions are as follows: - The technical feasibility of the whole chain of Route A – “reduction – selective oxidation – roasting – leaching/precipitation – FeV making” has been completely demonstrated. - The roasting, leaching, vanadate and V2O5/V2O3 preparation and FeV-making steps are successfully developed and proved in this project including a novel high temperature roasting (HTR) process has been developed. The innovation will shorten the roasting time by a factor of about 10. The vanadium recovery yield of the HTR roasted V-slag was up to 97%. - A novel oxy-chlorination process for direct roasting of high V-bearing BOF steel slag has also been demonstrated in laboratory scale with an overall vanadium recovery of up to 95%. In this process Cl-bearing wastes like PVC waste streams could used as the energy source and reagent. Further verification of this concept in larger scale is needed and recommended.
Keywords
Extraction, Minerals processing, Metallurgy, Recycling of mining and smelting residues, Metallurgical extraction
Consortium
- MEFOS (Sweden)
- FERROVAN (Finland)
- BRGM (France)
Duration
- 26 months (2014-2017)
Total Costs
- 1 203 234 euros
Total Requested
- 829 912 euros